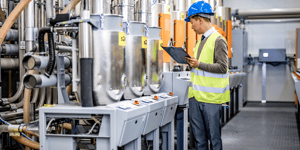
Work Smarter: Cut Costs & Boost Efficiency in Manufacturing
In today’s competitive landscape, manufacturing and distribution companies are constantly looking for ways to streamline operations, reduce waste, and lower costs—all while maintaining quality and meeting customer demand.
Whether you're optimizing workflows or leveraging technology, improving efficiency can lead to significant cost savings and a stronger bottom line.
Here are some best practices to help your business operate smarter, not harder:
1. Implement Lean Manufacturing Principles
Lean manufacturing focuses on eliminating waste—whether it’s excess inventory, unnecessary motion, or inefficient processes. Techniques like 5S (Sort, Set in Order, Shine, Standardize, Sustain) and Just-in-Time (JIT) inventory management can help reduce costs and improve productivity.
2. Automate Where Possible
Automation isn’t just for large-scale operations. Investing in robotics, AI, and smart software can reduce manual errors, speed up production, and improve accuracy in order fulfillment. Even small automation improvements—like barcode scanning for inventory management—can save time and labor costs.
3. Optimize Supply Chain Management
An inefficient supply chain can be a major cost driver. Consider strategies like:
- Supplier diversification to avoid disruptions
- Negotiating better contracts for bulk purchasing
- Using predictive analytics to forecast demand more accurately
A well-managed supply chain reduces delays, lowers costs, and ensures products move efficiently from production to delivery.
4. Reduce Energy Consumption
Energy costs can be a silent profit killer in manufacturing and distribution. Conduct an energy audit to identify areas where you can cut back—such as upgrading to energy-efficient equipment, optimizing HVAC systems, or implementing smart lighting controls. Small changes can lead to big savings over time.
5. Invest in Employee Training & Engagement
Your workforce plays a huge role in efficiency. Employees who are well-trained and engaged are more productive, make fewer mistakes, and contribute to process improvements. Implementing continuous training programs and offering incentives for efficiency-driven ideas can lead to a more innovative and cost-conscious team.
6. Improve Inventory Management
Holding excess inventory ties up cash and storage space, while running out of stock can lead to lost sales. The key is finding the right balance. Using an inventory management system (IMS) that integrates with your supply chain can help you track real-time stock levels and reduce carrying costs.
7. Streamline Logistics & Distribution
Transportation and logistics can be major cost centers. Consider optimizing your distribution network by:
- Consolidating shipments to reduce transportation costs
- Using data analytics to optimize delivery routes
- Partnering with third-party logistics (3PL) providers for cost savings
Efficiency in logistics translates to lower fuel costs, fewer delays, and happier customers.
8. Embrace Preventive Maintenance
Equipment downtime can disrupt production and lead to expensive repairs. Instead of waiting for something to break, adopt a preventive maintenance strategy to extend the lifespan of machinery, reduce costly breakdowns, and keep operations running smoothly.
Ready to Optimize Your Operations?
Efficiency isn’t just about cutting costs—it’s about creating a smarter, more agile business that can adapt to market demands. By implementing these best practices, manufacturers and distributors can improve productivity, reduce waste, and boost profitability.
Looking for more ways to optimize your operations? Our team can help. Get in touch today to explore solutions tailored to your business needs.
To learn more about LGT and how we can serve you, contact us here.
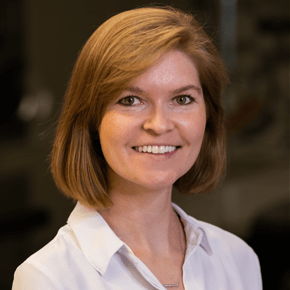